What is driving more interest in security systems?
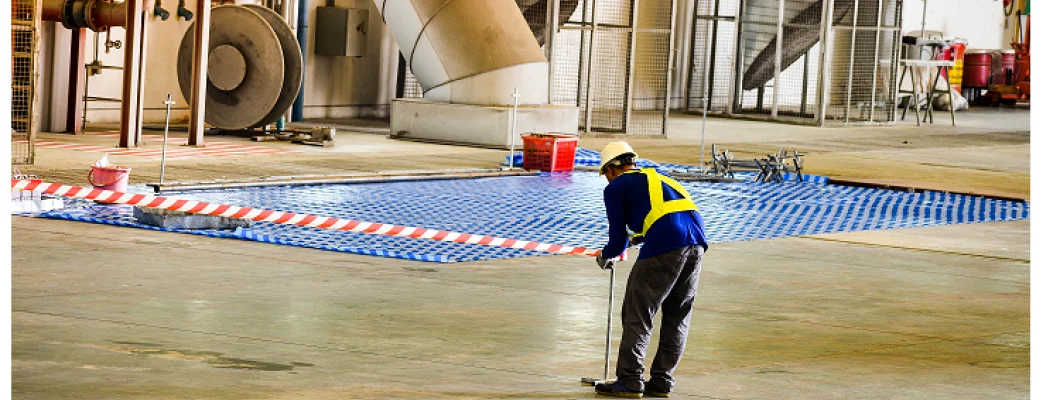
Industrial automation relies on safety systems
Industrial automation is a rapidly changing branch of technology. Systems integrators are currently seeing significant changes in their customers' understanding of machine safety and the need for secure systems. Security inquiries have increased. Increasingly, functional safety is being added to the forefront of control specifications. In the past, many customers viewed functional safety and risk assessments as just additional project costs that, in addition, put a significant strain on the project budget. They agree that risk assessments can be time-consuming, safety equipment can add cost, and the design process can be slow. All of these objections may be true, but there is now a noticeable positive change in the market driven by the need for security, but this is also due to the availability of functional security hardware and tools for system design and integration. There are plenty of options and features to solve whatever is needed.
Understand the system you have and implement the appropriate security systems and standards
The first step is to understand the system you have and the security requirements associated with that type of system. Some systems have specific requirements (for example, robots), while other systems are subject to more general requirements. Knowing which standards to address can be a challenge, but it becomes easier as your overall security knowledge increases. Working with a safety systems integrator or a safety-certified functional engineer can help identify requirements and relevant safety standards. Once the requirements are understood, a risk assessment approach can be defined to ensure that all risks are identified, assessed and mitigated accordingly. Considering this risk assessment early in the design process allows for the most effective mitigation (or elimination) of these risks with minimal impact on the overall project. With the latest technologies, safety control design has become much easier, and these technologies are highly integrated with standard controls. Safety I/O is distributed and integrated directly with non-safety I/O. Most control configurators allow the designer to easily select both safety and non-safety I/O as needed.
The goal of any safety control system is to protect operators from system damage
The risk assessment should determine the safety functions required for the system. Many of these functions are now a fundamental part of the control system software development package. Safety-enabled logic solvers (i.e. relays, PLCs, robots) contain predefined functions that can be easily configured to meet requirements. This reduces software development time, ensures a consistent program (reduces errors) and facilitates validation and verification. The goal of any safety control system is to protect operators from system damage. The advantage of today's controllers is that they all do this very well, but because they can be integrated at such a systemic level, it creates a design that is highly engineered and easier to operate and maintain.
Source: Plant Services
If you're interested in the topic of machine safety and want to learn more about what industrial devices can enhance process safety in your industry, take a direct look at the devices you'll find HERE. In addition to safety switches and circuit breakers, you will find safety lasers and scanners, as well as a whole range of relays. all devices are certified to work in strictly industrial conditions.
.